case studies
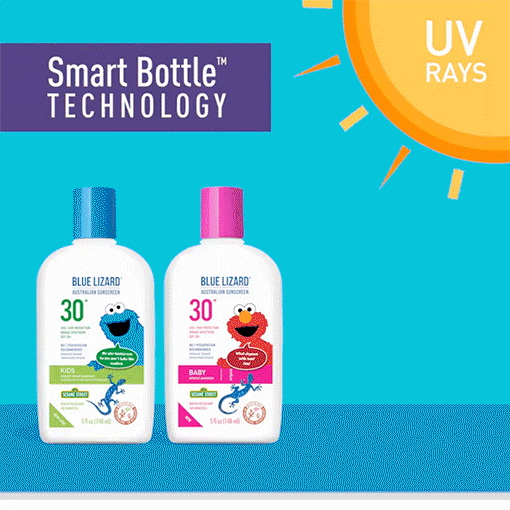
Photochromic Masterbatch
Challenge
The client was purchasing a photochromic masterbatch and experiencing a high rate of scrap loss. The manufacturer did not seem interested in accounting for or improving the excessive loss of material. The goal was to find another source of the raw materials and a manufacturer who could produce a masterbatch with reduced scrap amount.
Solution
We were able to find an analytical lab that was able to identify and quantify the additives in the current material. We then identified and quantified the photochromic colorant. Once all the raw materials were identified we were able to source all the materials and blended them in-house. We then sourced a compounder willing to produce the masterbatch using the blend we supplied.
Results
The ability to source all the raw materials needed, resulted in significant savings of the blended materials. A quality compounder reduced the scrap rate considerably, resulting in more finished compound available to produce parts.
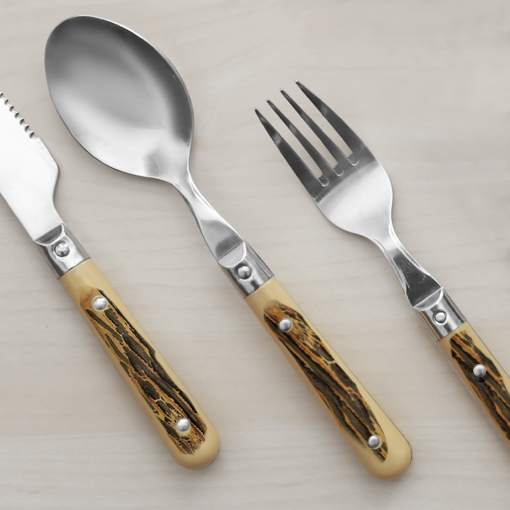
En Masse Coloration of
Molded POM Parts 1
Challenge
The client was having POM parts molded and subsequently colored (after the molding process) to achieve a specific effect on the final part. The molder made a business decision to no longer make these parts in favor of doing work for a larger client. Our client found another molder but they were not able to provide the post coloration process needed. If they could not do this process they would have to discontinue this product line.
Solution
We were able to set up a process where the client would send us the parts, we would source the colorants needed to achieve the shade, and we colored the parts.
Results
The trials worked so well that we continued the process for 5 additional colors. The client was able to continue making the product line. We were able to color anywhere from 10 part trials to over 10,000 part production runs.
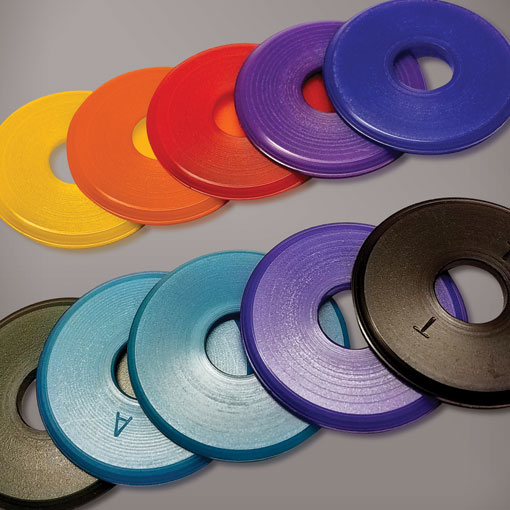
En Masse Coloration of
Molded POM Parts 2
Challenge
The client was manufacturing POM parts used for a new rivet removal tool. The client wanted to have the parts color-coded to use for different rivet sizes. Since these were being made in small batches the parts were machined and could not be made in different colors.
Solution
The client sent me sample parts so that I could test my dyeing process on them using a variety of colors. We were able to offer 9 different colors.
Results
The client chose 5 colors which we made until the business grew large enough to have the parts injection molded with color.
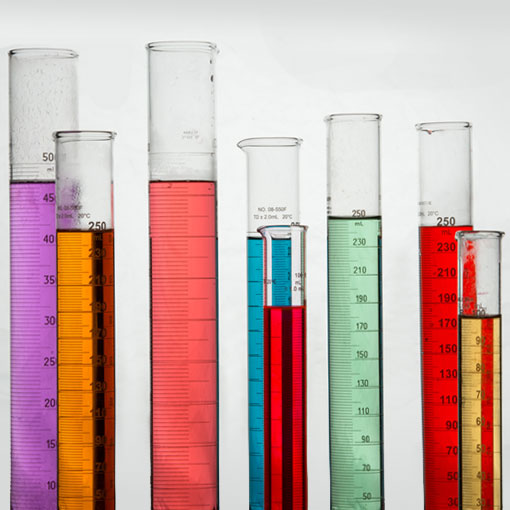
Palette Optimization
Challenge
A large manufacturer of cleaners and chemicals with over a thousand SKU’s was looking to streamline the number of colorants they purchase to reduce purchasing costs and raw material inventory.
Solution
We were given access to the inventory of over 50 SDS and datasheets from all the existing suppliers of colorants to multiple manufacturing locations. We were able to determine that they were buying the same product but in various strengths from several or in some instances the same supplier. In some cases, we needed to compare colors in solution in our lab.
Results
We were able to reduce the number of colorants they purchased by 20% and were able to make suggestions to formulations where colorants were removed from the palette.
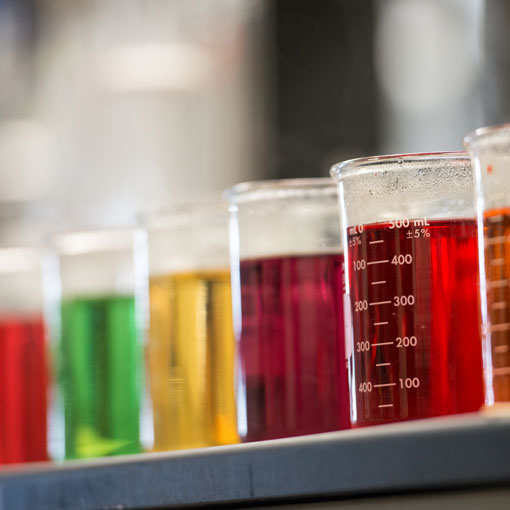
Color Stability Recommendations
Challenge
The manufacturer of a 2-part wood cleaner was having difficulty finding colorants for highly acidic and highly alkali components of their product.
Solution
Samples of the two components were sent to our lab to test a range of eight colorants known to be stable in extreme pH conditions. The colorants were let down in the samples and tested under heat for stability.
Results
One sample was found to be stable in the acidic component and 5 samples were found to be stable in the alkali components. Samples were supplied to the client for further long-term testing.